Bearings and grease
This article is intended to be a short crash course on grease in rolling element bearings that in the space of ten or so minutes will take you from scratch to knowing what grease to use in most common applications, how often and how much. Since 90% of applications are all going to use pretty much the same grease, we can do this without being exhaustive. There’s a lot I don’t cover but anything outside of a very basic, standard application is something you should talk to either your bearing or lubrication supplier about.
Why rolling element bearings need lubrication
Taking a deep groove ball bearing as an example, we have an inner and outer race with a ball rolling in between them. The two bearing races have a groove with a cross sectional diameter slightly larger than that of the ball that rolls between them. In theory, this gives us a point contact and ball rolls along that point and there is no sliding. However, Heinrich Hertz told us that under any load, the ball slightly squishes into the race and so now we have a little area of contact (see my crappy sketch below). Roll the ball now and we have rolling contact in the middle and sliding contact at the sides. It’s even worse with tapered roller bearings where the rolling elements aren’t cylindrical.
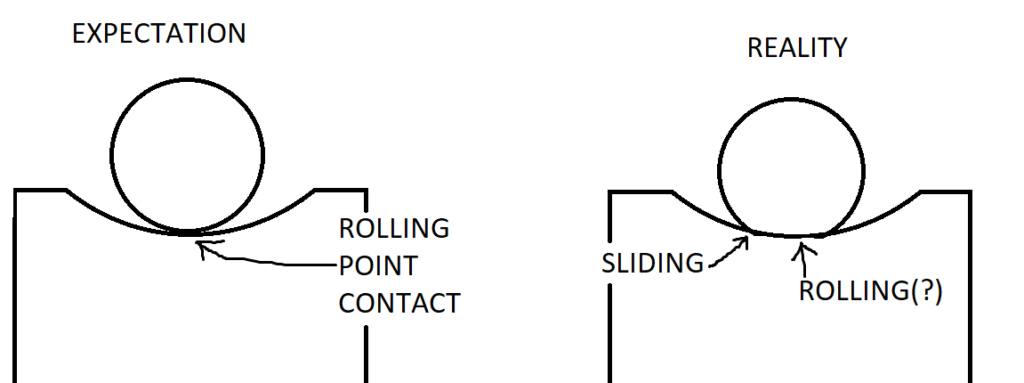
Since metal sliding on metal is bad news, we need to get a lubricant film in there or our bearing will soon convert itself to red dust. With a lubricating film in between the ball and the race, the sliding metal surfaces can glide over each other and the film can do the shearing as opposed to the metal doing it.
If we are lucky, we have budget for giant cast housings filled with oil and we get oil pumps and hardlines everywhere and temperature monitoring and the bearings will always have lots of oil to form a shear film with… But back here on earth with the rest of us, we generally don’t. Instead, we have grease.
How grease works
Grease is typically a fluid phase of an oil combined with a thickener. If you’ve done a bit of reading about it already, you’re probably already familiar with the analogy of grease being a bit like a kitchen sponge soaked with water. The thickener holds everything in place so the oil doesn’t immediately leak out through the seals and the oil is what does the actual lubrication. Wikimedia commons doesn’t have a picture for me to nick for this article and my microscope doesn’t magnify enough to take my own photo but in practice it looks more like a wad of waterlogged hair like what you’d pull from your shower drain.
When you take your new, greased bearing and run it up to speed, the rolling elements in the bearing are constantly ploughing their way through it, pushing it out of their way and it keeps returning to get underfoot like an oblivious toddler. This produces heat and is referred to as the “churning phase.” More on that later. After many cycles, it eventually settles in its place, out on the sides of the bearing and sitting on the cage.
From there, the grease “bleeds” oil onto the rolling elements and track over time which, again, is what does the actual lubrication. There’s a secondary mechanism where the “hair” or “sponge” structure of the grease breaks down at higher temperatures which gives a negative feedback against overheating- When the bearing gets hot, the grease breaks down, releases oil and (hopefully) lubricates the bearing which cools it down again.
The above, by the way is a very short summary of my understanding of the first couple of chapters of Grease Lubrication in Rolling Bearings by Piet M. Lugt.
Grease and it variants
As there are multiple components to grease, specifying it can be rather confusing. referring to our earlier analogy analogy of grease being a bit like a kitchen sponge soaked with water, let’s talk about the sponge part first.
Thickeners
The consistency of the grease overall is commonly specified by the NGLI number ranging from 000 (tomato sauce) to 6 (hard cheese). There’s lots of articles on the internet about exactly what number is equivalent to what common substance that I won’t replicate. This overall consistency affects the tendency of the grease to stay where you put it. It is not the same as the base oil viscosity which is a separate, independent thing.
Choosing thickener consistency is generally a function of temperature and speed- here’s a good guide. There are sometimes other factors, such as pumpability if you are running a central lubrication system and there are, of course, lots of weird corner cases for which you should be talking to an expert.
The thickener type is typically specified by environmental factors like temperature and ability deal with water. For example, lithium thickeners are the most common but when you need to deal with high temperatures or water ingress, polyurea might be a better option. Here’s a couple of articles about choosing thickeners- Soap thickeners and Non-soap thickeners.
Base oil
Base oil viscosity, is the measure of the viscosity of “the water in the sponge.” The base oil is what actually gets between the sliding bits of metal in our bearing and enables them to glide over it. It is selected based on bearing surface speed and operating temperature. SKF have a good article on how to figure out what you want here. If you play around with this calculation for a bit, you’ll see there’s no magic number but rather a large range of “she’ll be right.” for example, a bearing with a mean size of 100mm running anywhere between 100RPM and 5,000RPM at 50 degrees Celcius will be OK with anything from ISO 68 to ISO 680 base oil viscosity. It’s only when you go into extremes that you really need to think about it. Again, referring to the SKF guide, our 100mm bearing requires us to go for a thinner oil if we start venturing above 5000RPM to keep the temperature from getting too high or add AW or EP additives if we are below 100RPM.
Just to highlight the difference between the two above points -in high speed bearings, a thinner, less viscous base oil is required but a “thicker” NHLI number is more appropriate. You can vary these two parameters independently. The idea here is that the thicker overall consistency will help to reduce churn on run-in as the grease will tend to stay in its place a bit more – around the cage and the sides of the raceway. Meanwhile, the base oil that will hopefully end up in the track is nice and thin and won’t get overly hot by being sheared around by the interactions between the balls and the races.
Greases are often specified by DIN 51502 and ISO 6743-9 and here is a good guide on that nomenclature. The same website also has a good article on grease selection here.
If you are looking into this and find you need anything other than Mobil XHP-220 series or Castrol Spheerol EPL series, it’s time to either spend the next week reading or call your supplier (protip, if you are doing this for anything other than your own personal enjoyment, the correct move is the latter). These are both Lithium-thickened, Mineral oil greases available in NGLI 0, 1 or 2 (I used to use 2 typically).
Calculating greasing intervals
This is pretty well documented and calculations can be found on most bearing supplier’s tech manuals as well as most grease manufacturers, too. For example, FAG use bearing type times the speed in RPM times the mean bearing size which gives you a value you can look up on their chart (figure 33 in Rolling bearing lubrication or alternatively, Mobil have a nice chart which requires no math at all. Of course, these guides come with a lot of caveats and fudge factors for things like high speeds, temperatures, etc, etc.
To take an example, a 100mm ball bearing running at 1000RPM gives us 20,000 to 80,000 hours of operation or somewhere from 2 to 9 years, assuming 24/7 operation! When speeds are low, it seems you can get away with a lot. Having said that, I can’t imagine purposely leaving a bearing to fend for itself for so long, especially given the following:
The consequences of too much or too little lubrication in real terms
The consequences of under-lubrication are pretty self-evident. Once you’ve leached out the available base oil and your lubrication film is all but gone, friction between the sliding metal heats it all up. This runs away in very short order and causes failure. But what about over-lubrication?
You can’t read a modern document about lubrication without being told that over-lubrication causes more bearing failures than any other cause which is a BS statement in my view. The failure mechanism for over-lubrication is that if there is too much grease, it never stops churning and in a fast moving bearing the heat from churning gets so high that it completely breaks down the grease during run-in, at which point you’re basically running an unlubricated bearing except it’s hotter. This, of course is very bad news and will definitely kill your bearing in short order.
However- and this may just be bias from the equipment I’ve dealt with in the past- most bearings aren’t running so fast to cause this issue. It’s certainly my experience that most bearings smaller than 100mm at less than 500RPM can be greased until the grease is oozing through the seals on both sides without consequence as long as the seal isn’t forced off entirely. Note, I’m not saying this is a good or smart thing to do. It’s messy, it’s poor practice and it makes you look sloppy. Since this is likely to be a controversial paragraph, I’ll quote the FAG manual directly:
Large relubrication amounts are recommended with large free housing spaces, grease valves, grease escape bores, or with low speeds corresponding to n · dm ≤ 100 000 min–1 · mm. In such cases, the risk of temperature increases due to working of the grease is reduced.
ROLLING BEARING LUBRICATION, FAG Kugelfischer Georg Schäfer AG, Publ. No. WL 81 115/4 EA
How much grease do you put in?
SKF and FAG have a similar approach- the amount of bearing grease in grams to put in is a factor of bearing size. SKF state 0.002 x D (Bearing OD) x B (bearing width). FAG say the same for weekly regreasing but 0.003 x D x B for monthly and 0.004 x D x B for annual regreasing. An average grease gun will give 1-1.5 grams per pump (measure yours if you’re feeling antsy about it) so going by those numbers, a 100mm OD x 25mm wide bearing greased weekly should take roughly 4 pumps.
Intuitively, that seems quite a bit for a high speed bearing so how can we sanity check that? The old maintenance engineer’s trick that my team taught me was to- if possible- lubricate while running and only pump until you notice a decrease in noise. This is made easier by the use of a stethoscope. Potentially, you could also monitor temperature in order to stop pumping in grease as you begin to experience churning but I won’t pretend that I’ve done it so I can’t say how effective this method is.
Summing up
On reflection, after reading online articles and manuals about bearing grease one tends to get the impression that some sort of scientist in a lab coat should be carefully testing, checking and specifying all these grease parameters and each bearing should have its own interval and replenishment quantity and run-in procedure… But after going through the calculations, it seems that for almost every bearing I encountered working in a paper bag plant, a guy in a cowboy hat can stroll in once a year, give each grease nipple four pumps of XHP222 and be done with it.
I typically had quarterly-or-so re-greasings that probably could have been annual, though greasing them more often wouldn’t have caused any harm. The overgreased bearings probably didn’t suffer, as unsightly as it was and the non-serviceable bearings could be expected to last 2-9 years, as anyone with 2-9 years of experience in that field probably already knows. The Mobil XHP222 that was used on almost everything was a good choice though knowing what I know now, I would have used a thinner NGLI grade in the automatic lubricators.
At least I’m not intimidated by DIN grease codes anymore. Until next time, have fun and keep them greasy.