Pillow blocks
I’m lazy. I don’t like figuring out bearing seat tolerances if I don’t have to. I also relish in avoiding figuring out how to get bearing seats coaligned and while I love fresh, new bearings, I loathe pressing them in. I particularly hate repairing damaged bearing seats. That’s why I love pillow blocks. In this article, I sing to their praise.
What they are
There are many variants but let’s start with the most common type. Start with a standard deep groove ball bearing but make the outer race spherical. Because of the spherical outer race, you can mount a shaft in two of these bearings and when they are mounted on an uneven surface, they will align themselves in their housings to suit. This means you don’t need a particularly flat or coplanar pair of surfaces to mount these on as long as you don’t mind your mounted shaft being at a very slight angle.
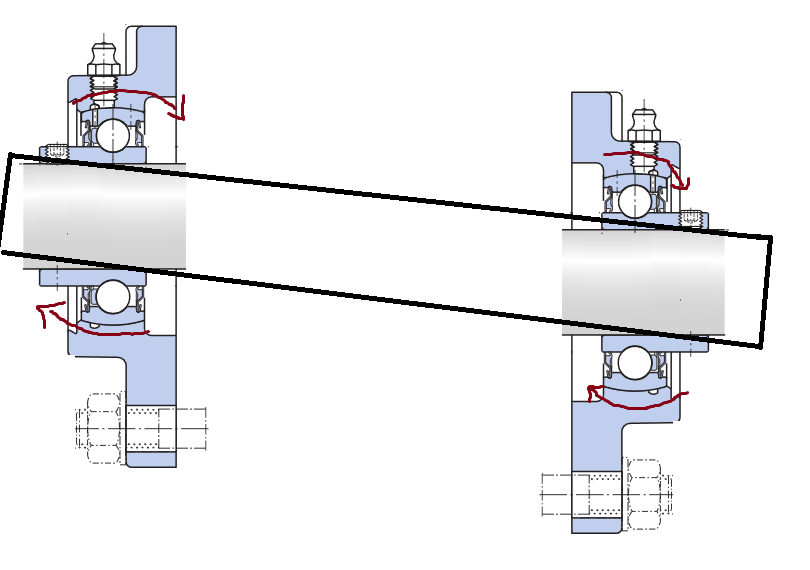
The housings themselves are most commonly cast iron though you can get pressed steel and plastic ones. They come in a variety of mounting methods, the most common being two and four bolt flange mount and the two bolt normal mount shown below.
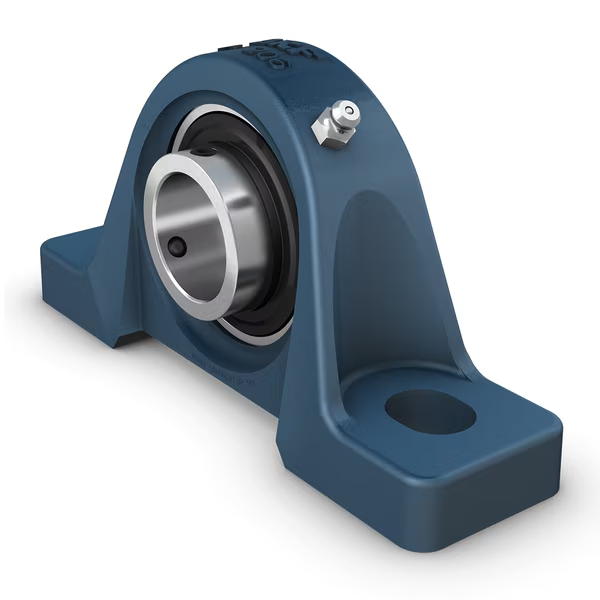
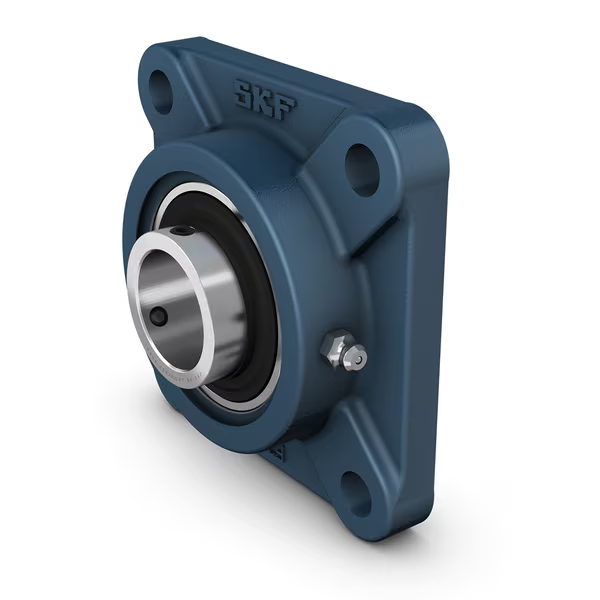
There are other varieties that come in handy for specific applications that are worth knowing about. For example below. On the left is a take up unit from Schaeffler intended to be tensioned by loosening the bolts slightly and jacked with a bolt or screw. In the middle is an SKF unit that can be mounted in a large cutout. On the right, the same thing is achieved with a laser cut plate.
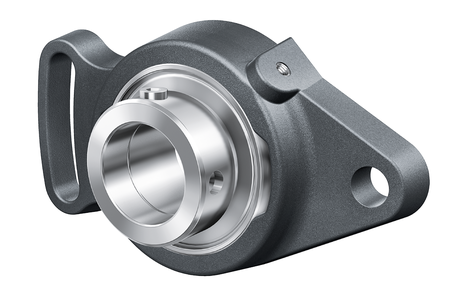
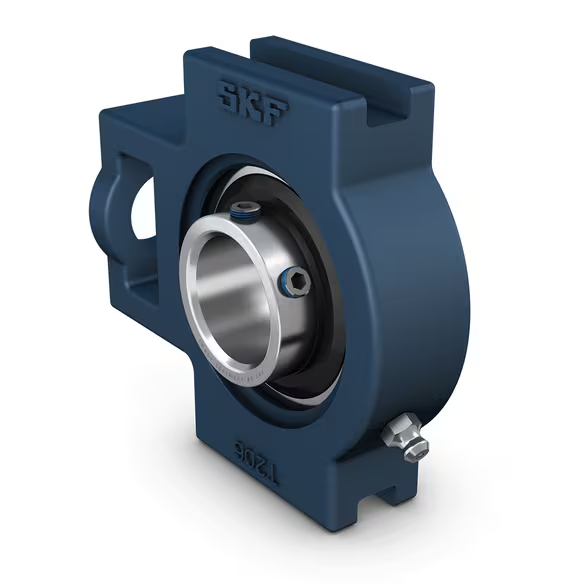
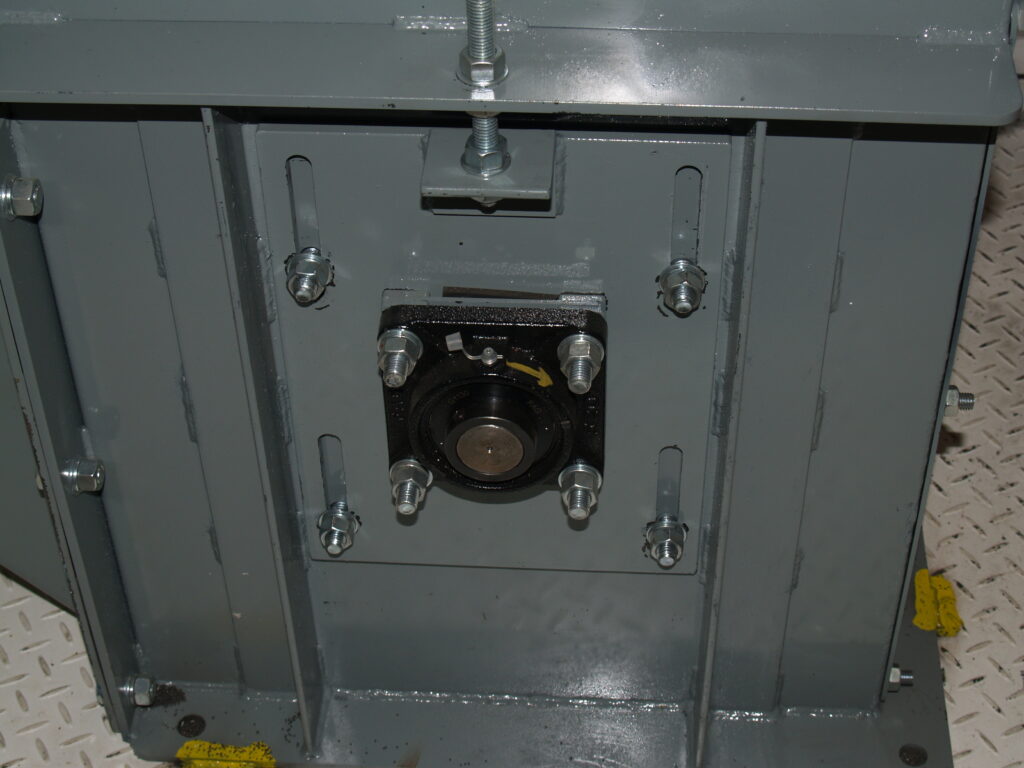
There are a slew of other varieties including very large and heavy duty types with roller bearings, self aligning roller bearings, plain bearings and many more.
Interchangeability
You can generally chop and change between manufacturers if you are careful with your part numbers. For example, Schaeffler’s GRAE50-XL-NPP-B can be replaced with SKF’s YET 210 or NTN’s AEL210. You can generally interchange the inserts in the housings and the housings from one brand to another. I say generally because you should always check as there can be small differences.
Recovering from mistakes
You can buy both imperial and metric bearing inserts for your housing and also with or without adaptor sleeves which gives you a few more options to recover from a screw up. For example, say you have a YET-207 in your design. This is a fairly common insert bearing with an eccentric locking collar for a 35mm shaft. The shaft that this mounts on has either been damaged or made undersized. The following bearings have the same outer dimensions and can be swapped over, allowing you to only machine the shaft:
- UC306 (30mm shaft, set screw locking)
- YSA-207-2FK (tapered adaptor sleeve for 30mm shaft)
- YET-207-105 (eccentric locking, 33.338mm shaft)
- YET 207-106 (eccentric locking, 34.925mm shaft)
While I don’t typically advocate for the use of imperial bearings where everything else is metric, desperate times call for desperate measures and having an option like this can really save your skin.
Axial location
As with all bearing setups, you need to consider axial location. Fortunately, there are a number of options that can be included.
The cheap and most common type simply has two grub screws that press onto the shaft. This isn’t particularly strong but if you remove the grub screws and dimple the shaft and reinsert the grub screws, they can take quite an impressive amount of axial load. You should feel no shame in doing this.
If you shaft is turning in one direction only, eccentric locking collars are a good option. They have a grub screw that interfaces with the shaft also but this grub screw turns an eccentric step that tries to misalign the collar and the bearing bore, binding them to the shaft.
If your shaft turning direction is not constant, concentric locking collars are an option, as are tapered shafts. Of course, you can also just sort out your own axial retention as you would with any other bearing setup.
Cost
Pillow blocks are so damn cheap for what they give you. It’s not just that the bearing unit itself is dirt cheap- You don’t need to post-machine your weldment because of their self-aligning nature. You don’t need to machine bearing seats. You don’t need to drill greasing channels or buy grease nipples. You don’t need any auxiliary retention. Mounting them is fast and requires less skill and is therefore cheap also.
Serviceability
Pillow blocks of all kinds are fantastic for serviceability- provided you use them appropriately. See the example below. This is a quick sketch of a conveyor assembly featuring two crowned pulleys on a shaft mounted between two chassis plates. With this assembly, in order to replace one or both of the pulleys, you need to demount both bearings and both pulleys as they are on the conveyor, slide (hammer) out the shaft and reassemble in situ. This type of service involves crouching, kneeling or lying on the factory floor with a machine down waiting for you. Not pleasant.
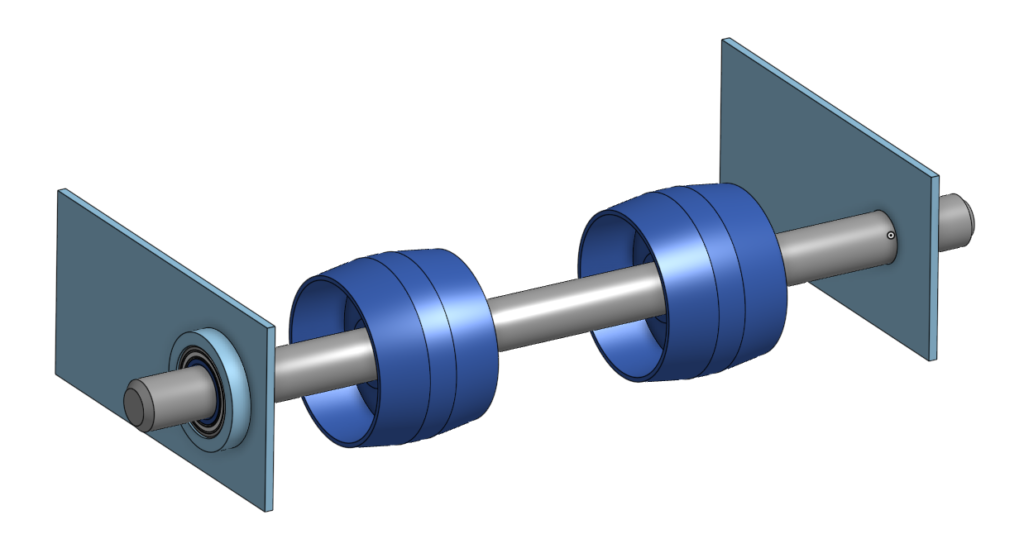
The same setup with appropriately designed pillow blocks can be removed and taken to the workshop by simply unbolting one pillow block. Servicing the bearings is also easier this way- You don’t need to mess around with bearing retainer nuts or circlips and you don’t need to worry about pulling or pressing bearings out of their seats- Just loosen a couple of grub screws and the main bolts of each pillow block and lever it off. Then you can replace the insert and reinstall.
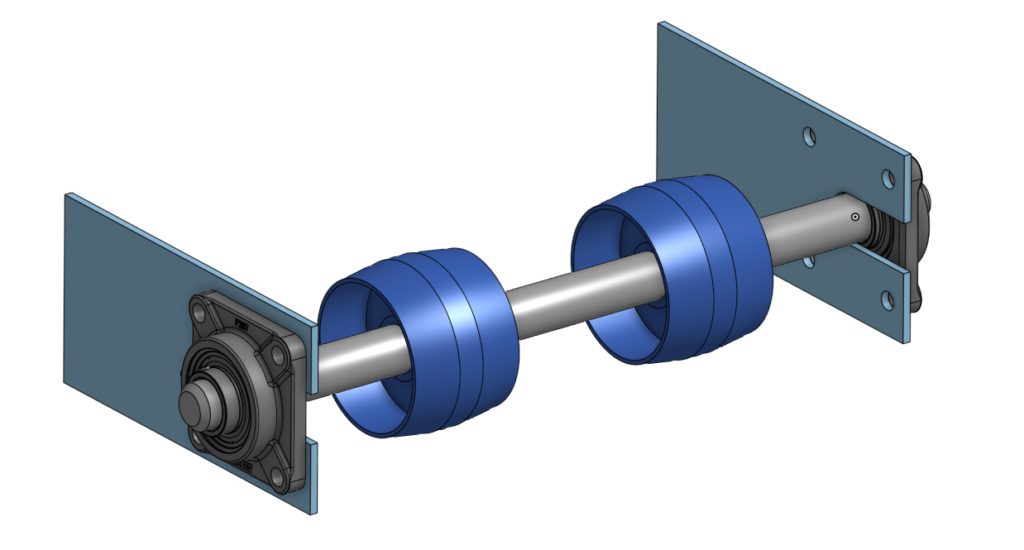
Note that in order to tension the belts, you could use one of the take up units shown earlier in the article.
When not to use them
They typically don’t have a place in racing and aerospace applications as they are heavy and they are not suitable in applications where a spindle needs to be located accurately as they lose their position once their mount bolts are loosened. They are bulky so don’t work well in tight installations.
Conclusion
There are very few products out there that hit all three corners of the fast-cheap-good triangle and these are one of them. Use them and enjoy the four hours that you don’t have to spend thinking about machining bearing housings.